
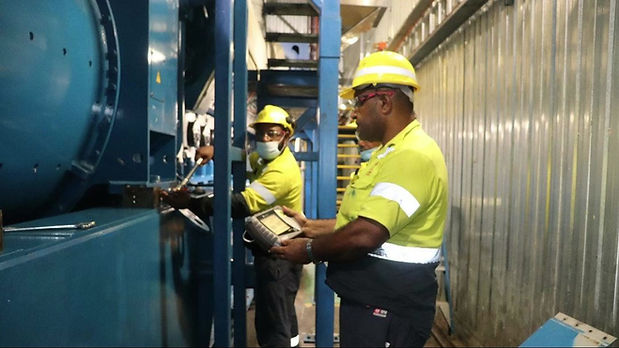
Key Aspects of Thermography Inspection
During a thermography inspection, our engineers and technicians utilize infrared cameras to detect and analyze heat patterns on surfaces. This process enables them to identify potential issues within a system by observing temperature variations that may suggest problems such as faulty electrical connections, insulation defects, mechanical failures, or structural weaknesses. Essentially, it provides a visual representation of heat distribution, allowing for the diagnosis of potential issues before they escalate.
Infrared Imaging
The main tool used is an infrared camera, which captures heat radiation emitted from surfaces and presents it as a thermal image on a display.
Temperature Analysis
Inspectors analyze the color differences in the thermal images to pinpoint areas with significantly elevated or reduced temperatures compared to their surroundings, which may indicate underlying issues.
Targeted Inspections
Thermography can be applied to various systems, including electrical panels, building envelopes, HVAC systems, industrial machinery, and more, depending on the specific goals of the inspection.

What a Thermography Inspection Can Detect
Thermography inspections use infrared technology to detect hidden issues before they become costly failures. By identifying heat variations, they help pinpoint electrical faults, energy inefficiencies, mechanical wear, and structural concerns. This proactive approach improves safety, reduces downtime, and enhances efficiency across various industries. Here’s what a thermography inspection can uncover:
Electrical Issues
Overheated connections, loose wiring, and failing components within electrical panels.
Building Energy Loss
Inadequate insulation in walls, windows, or doors, as well as air leaks.
Mechanical Problems
Defective bearings, misaligned shafts, and overheating in motors.
Structural Concerns
Moisture intrusion, water damage, and areas of heat loss in buildings.